RFID Marker Tag Locates Inventory for Women’s Fashion Company
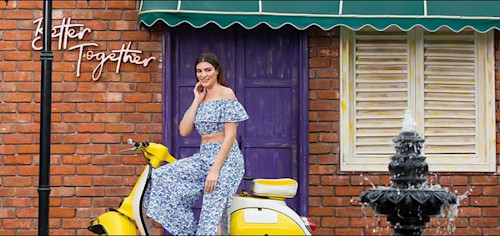
Advance Apparels, a women's fashion company that sells wholesale garments made at its two factories in India, reports that it has gained an accurate view of the goods within its warehouse as it has expanded its delivery models from wholesale to retail. The company, which has adopted a UHF RFID solution from SimplyRFID that is low-cost and easily deployable, is using the technology to identify where each carton of goods is located at its Hackensack warehouse. The solution leverages SimplyRFID's new Marker Tag product, which identifies the warehouse rack or shelf on which tagged goods are stored.
SimplyRFID's Wave iOS app links each inventory tag with a Marker Tag to create a location for all tagged goods for Advance Apparels. The company offers more than 6,000 stock-keeping units (SKUs), ranging from tie-dye umbrella dresses and blouses to beach clothing and African or Ankara fashion. It operates two warehouses in New Jersey, one in Hackensack and the other in South Hackensack, according to Akash Bajaj, the company's director.
Until recently the company sold its products through wholesale markets, but more recently it has begun dropshipping for retailers, as a service provided by a third-party supplier. The company stores inventory for the retailer and ships it to a buyer that makes purchases from the store's website. Advance Apparels' products are also sold at beach stores and boutiques. Most stores that carry its goods are small businesses, the company reports. And last year, during the COVID-19 pandemic, Advance Apparels opened a direct retail website.
Customers are already signing onto the new site after seeing garments in stores and making direct purchases. "We've had a lot of traction on our website." Bajaj says. "That's going to be a big part of our business going forward." By diversifying, however, the company now has a more complex system in its warehouses. As a result, storing and then locating goods, as well as understanding inventory counts in real time, has become more challenging. Additionally, because Advance Apparels serves small businesses rather than large-box retailers, orders can be small and require the opening of multiple cases and the removal of small amounts of product.
The South Hackensack warehouse is the smaller of the two, measuring approximately 14,000 square feet in size. The technology has been taken live at that location, with the 22,000-square-foot Hackensack facility slated to follow in the fall. The Hackensack site was chosen for the first deployment because as the main fulfillment center, it has the largest amount of inventory turnover. When it comes to counting inventory manually, Bajaj says, "There's been bad information over the years," but this has improved in recent years, he notes.
The labor associated with knowing what inventory is onsite and where it is being stored has been exhaustive, Bajaj says. Since the company provides wholesale, retail and dropshipment for other retailers, he explains, "The complexity is tough to handle in the system." The RFID solution is designed to track goods at the case level. Typically, there are 48 units in each case. Due to the relatively low value of a single garment, he says, "It doesn't work out to track per garment, yet." However, the company intends to eventually transition to item-level tracking.
The solution consists of Convergence Systems Ltd. (CSL) CS108 handheld RFID readers that are attached to forklifts or carried by warehouse workers. Inventory levels are captured as the vehicles travel through the aisles, as well as by individuals walking with a reader in specific areas. Advance Apparels uses four levels of racking on which pallets of goods are stored. The bottom two shelves are dedicated to loose merchandise, with no RFID-based tracking performed. Pickers take their picking orders, walk through the racks and reach into cartons to retrieve the items required to fulfill each order.
The top two racks contain full cartons that are tracked via Avery Dennison AD229 inlays, each on a 4- by 2-inch label. SimplyRFID provides the finished, encoded product. Each passive UHF RFID tag is affixed to a carton upon being received from the manufacturing site in India. The unique ID number on the tag is linked to the SKU data in SimplyRFID's cloud-based software and Wave app. The app lets users view the data on their Apple iPhone and pair it to the handheld reader.
After the goods are put away, they will be periodically identified via handheld or forklift-mounted readers. The Marker Tags can then automate the location data. "A Marker is really a breadcrumb of where an RFID-tagged item has been," says Carl Brown, SimplyRFID's president. "When our (Wave) RFID handheld software sees an RFID Marker tag near an RFID-tagged item, it adds a trail—a history—of where an RFID tag has been." Thus, an item's location might be "Warehouse1," while the Marker's location may be "Shelf 5, Row 15."
As forklift drivers perform their normal rounds, they scan all RFID-tagged inventory, view the nearest Marker Tags and update the Marker locations for those items. The Wave software captures each Marker Tag's ID, along with the ID of every tagged carton, and stores that location information. Thousands of Marker Tags can be defined and placed throughout a warehouse to dynamically update RFID tag positions as tagged goods move throughout a company. The Wave software notes the new location of an inventory tag each time it detects a new tag and marker combination.
When Advance Apparels' inventory is replenished on weekends, workers make use of the RFID reader as well. They can view the location of each carton and move product to the lower shelf, to be accessed by pickers during the following week. The software updates each carton's status as it is moved, and it can prompt replenishment orders from the factory. Any leftover cartons that are moved to the recycling area can be scanned as well to indicate that a box is empty.
SimplyRFID found commonality in the women's clothing company's needs, Brown says. "Advance has the typical issue: SKUs at the case or pallet level and needs for a put-away process at multiple locations," he states. "They aren't massive and can't use robots, like Amazon. Wave is a great fit, because we can manage cases and give them rollup totals at the case level of product availability."
Additionally, the solution was customized to account for times when printing RFID tags would not be realistic. That feature resulted due to a request from Bajaj.
SimplyRFID encodes bulk tags, assigning 20 tags at once to a single SKU. This feature, Brown explains, "helps the company when it is not using a printer system. "They can use a pre-encoded tag and scan a bunch," he says, "and turn them into whatever they want. This is a useful feature now for many customers."
Before deploying the technology earlier this year, Bajaj recalls, Advance Apparels did not fully trust the inventory information it had regarding its warehouses. In many situations, the company had to order goods it didn't need since they could not be found. What's more, employees sometimes had to search the warehouse before placing orders to confirm that the specific items they needed actually had to be replenished. The RFID solution, he says, reduces the need for such manual checks and prevents both out-of-stocks and over-ordering.
After examining the RFID solutions available, Bajaj says, he chose SimplyRFID for its ability to solve problems affordably. "When I looked at all the RFID solutions," he states, "this looked like the easiest to get up and running, and the least expensive. The Marker Tag is one of the things that stood out for us. It cut our time searching by a ridiculous amount of time." The system, including the Marker Tags, has been in place since this past February. Once fixed readers are deployed, the Marker Tags will still provide benefits within the warehouse, he says, adding that the solution also opens doors for expansion, such as adding West Coast fulfillment centers.
In the meantime, SimplyRFID has been testing the Marker Tags in-house for the past nine months, and has been working actively with customers since the spring. With the Wave app, the Marker Tag data provides audit reports of what stock was on which shelf based on the tag data, as well as when it was there, and it can push that data to ServiceNow, QuickBooks and other enterprise resource planning systems.